Food Safety Compliant Inks and Digital Print: What You Need to Know
A Brief History of U.S. Food Packaging Regulation
Up until the 20th century, there were few federal laws regulating the food packaging industry in the United States. Standards and guidelines slowly developed over time in response to growing health concerns and public outcry for safe production and manufacturing practices.
Formal federal regulation began with the 1906 Pure Food & Drug Act, enacted to protect consumers against adulteration of food and from products identified as healthful without scientific support. Following came the Federal Food, Drug, and Cosmetic Act in 1938, giving authority to the U.S Food & Drug Administration (FDA) to oversee the safety of food, drugs, and cosmetics.
The Role of the FDA in Packaging and Labeling
Tasked with the important job of regulating packaging and labeling — the FDA sets strict standards for food packaging to protect and enhance consumer safety and confidence. Along with food labeling requirements such as nutrition information, expiration dates, safe handling and preparation instructions, the FDA also regulates any packaging elements that come into direct contact with food.
The Importance of Ink in Digital Printing
Ink plays a vital role in digital print for packaging and display. Brands must ensure the right ink is being used for each job based on the print surface, product, and end user to avoid potential risks. Different inks are used for different types of packaging applications based on their unique properties and chemistries, and the type of ink used is often tied to the specific press machinery.
Digital Print: Is it Food-Safe?
Digital print is a direct printing process where ink is applied straight onto the substrate — no print plates required. This provides the advantage of full-color graphics, variable data, and quick turnaround times. However, not all digital print technologies are food safety compliant for primary packaging applications based on their ingredients and drying methods.
UV-Curable Inks vs. Water-Based Inks
Some digital presses utilize UV-curable inks, which are exposed to ultraviolet lights immediately after being printed onto the packaging substrate. This curing process turns the ink into a durable polymer film, which doesn’t absorb into the substrate. While this process delivers durability, water resistance, and color consistency, UV-cured inks are not suitable for primary packaging applications where the packaging has direct contact with food, due to potential ink migration risks. If the inks aren’t fully cured during the production process, they can migrate into the corrugated fiberboard or other packaging materials and potentially contaminate the food product within if no additional barrier is present, such as plastic. Ink migration can lead to serious public health and safety concerns and put both consumers and brands at risk.
Enter: HP True Water-Based Inks.
These low-migration inks are nontoxic and completely free of UV-reactive chemistries. They meet stringent global food packaging standards, including FDA, EU Framework, Nestlé Guidance, and Swiss Ordinance, making them food safety compliant for use on packaging surfaces that do not come into direct contact with food. This opens the door for digital print to be used in a variety of primary food packaging applications, such as the outside of pizza boxes, produce trays, and dry food goods folding cartons without the need for an additional barrier.
Powered by digital print, food safety compliant inks enable brands to create high-quality, effective packaging while maintaining consumer safety and compliance with global food packaging standards. This is why The BoxMaker has invested in two HP PageWide C500 Presses, which use HP True Water-Based Inks*.
Environmental Impact
Water-based inks also reduce the environmental impact of food packaging by eliminating the need for additional materials, films, or barriers previously required to prevent contamination caused by ink migration. At the same time, UV-curable inks are evolving to become more environmentally friendly by using LED technology for curing, which is more energy-efficient than previously used mercury lamps.
Learn More About Digital Print and Food Safety Compliant Inks
To learn more about digital print applications and food safety compliant inks, we invite you to explore BoxMaker University, our on-demand library of webinars and classes specifically designed to help you increase your packaging knowledge and develop a winning packaging strategy for your brand.
Consult with Packaging Experts
The Packaging Advisors at The BoxMaker are here to answer any questions you may have about inks and guide you through your next packaging project. Choosing the right ink depends on various factors such as your specific packaging application, substrate, production method, order volume, and the press machinery used by your packaging manufacturer. Contact our team today to discuss the right solution for your next project.
*Please Note: The BoxMaker is not an FDA certified food packing facility and cannot guarantee that products produced in our manufacturing plants are FDA approved.
Subscribe
Share this post
Similar Articles
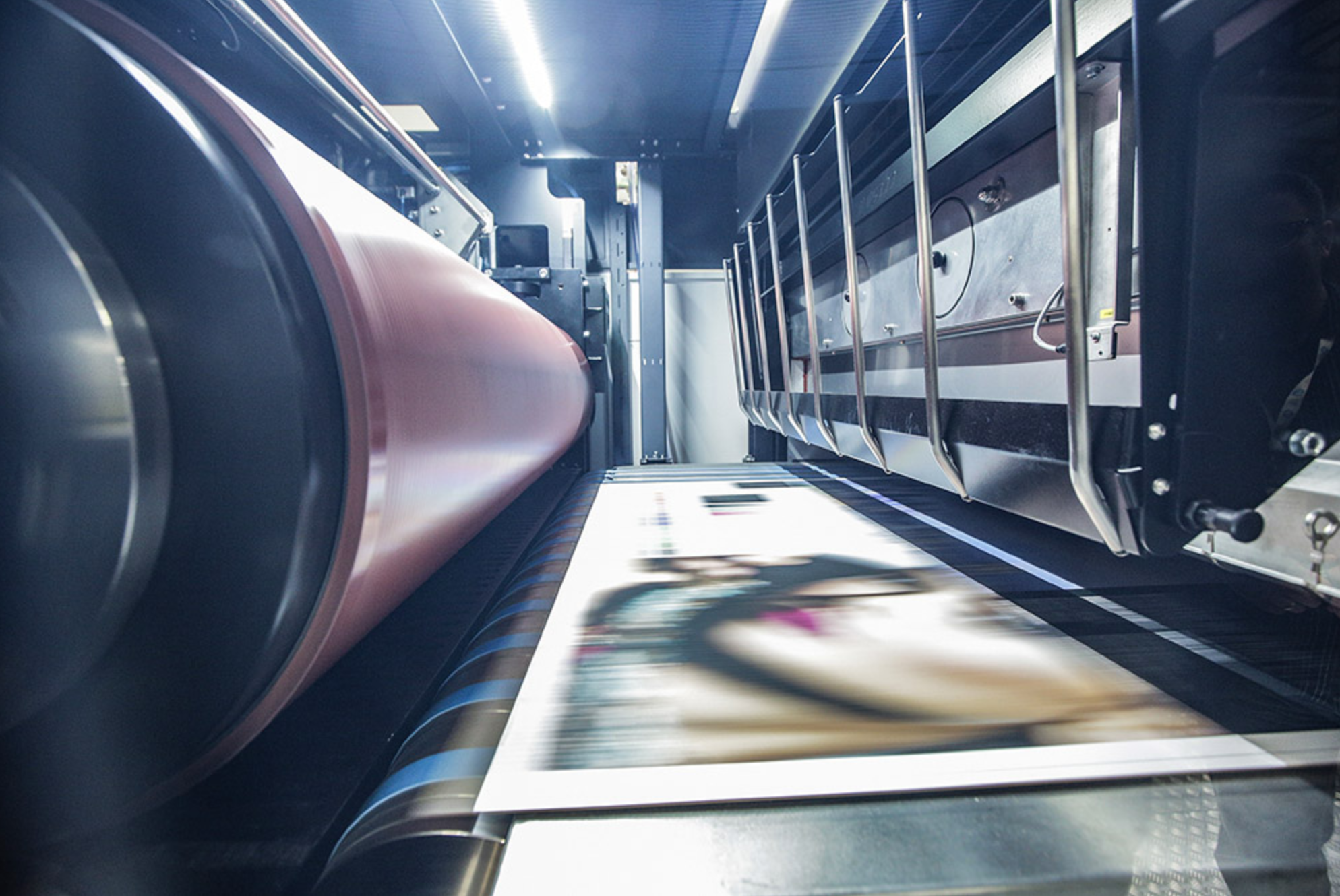
Meet the HP PageWide C500 Digital Press
Learn about the HP PageWide C500, a digital press for corrugated packaging and display that delivers …
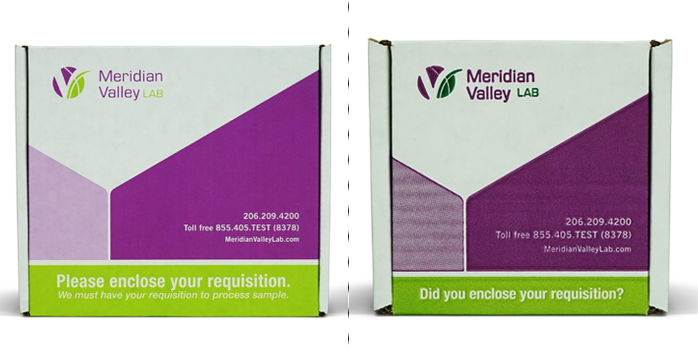
Making the Upgrade from Flexo to Digital Print
Switching from flexo print to digital print is no easy decision. Here are three reasons to make the …
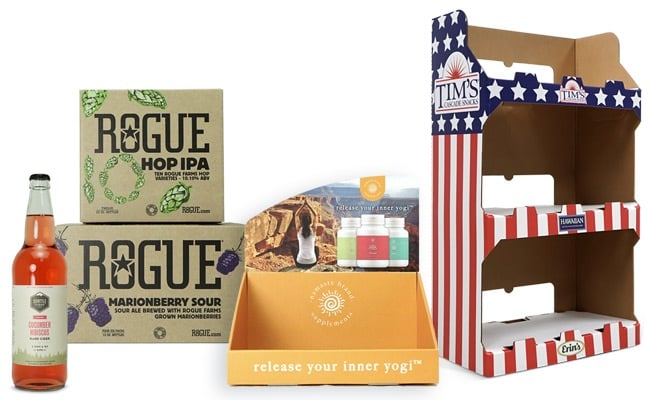
Litho Lamination vs. Digital Print for Retail Packaging
Learn about comparing Litho Lamination vs Digital Print and how technological advancements in digita …