Understanding the Layers of a Custom Label
Custom printed product labels are everywhere. Take a look around, and you may notice them on beverages, candles, lip balms, and much more. Pressure-sensitive labels leverage print to convey product information and to help shoppers choose between brands. Labels blend in with the object they are affixed to and are viewed by the consumer as a seamless part of your product.
Because custom labels are viewed as a reflection of your brand, the materials they are made of are just as important as what you choose to print on them. Your label must stand up to the many environments that it will experience as your product travels from warehouse through shipping and distribution, and finally, to its end destination and your customer. The label must remain intact through temperature changes, potential exposure to moisture, UV rays, friction, and more.
A custom product label is typically made up of four layers, each with a specific purpose. To better understand how product labels work, let’s peel back the layers of a label and discuss how each component plays a critical role in a pressure-sensitive label's overall performance.
Layer #1: Liner
The liner, also known as the backing or carrier, refers to the bottom layer of the custom label. The liner enables the label material to feed through the printer without any damage or resistance. The liner also protects the adhesive through the production process until the label is ready to be applied. A silicone release agent coats the liner to allow the end user or a labeling machine to separate the label easily from the liner.
There are three types of liners typically used: white paper liners, Kraft paper liners, and clear polyester liners. While all three liners can be applied either by hand or by machine, each has unique qualities to consider when choosing a liner.
White paper liners are the most economical option and thus are the most common. However, this type of liner is not recyclable. Although Kraft paper liners have a natural look, they are also not recyclable. This is because the paper liners have to be coated and become "mixed material" items, which are not easily processed at most recycling facilities. Clear polyester liners are most efficient to produce, and are the only option that is recyclable.
Layer #2: Adhesive
For a pressure-sensitive label to effectively stick onto a product, an adhesive layer is required. The adhesive forms a bond between the label and the surface it is applied to, providing the ‘stickiness’ needed for the label to adhere. There are four common types of adhesives: permanent, removable, cold/freezing temperature, and all-temperature. The type of adhesive required depends on the environmental conditions that the label must withstand, such as extreme temperatures and moisture.
As its name suggests, permanent adhesive is used for one-time label applications. Permanent adhesive forms a strong and durable bond between the label and the surface. If the label is removed, it will likely leave a sticky residue, or the label itself might tear. On the other hand, removable adhesive provides a minimal, temporary bond and can be removed and reused.
Brands in the food and beverage industry often use cold/freezing temperature adhesives for products that require refrigeration. Finally, all-temperature is a general-purpose adhesive designed to withstand a range of environmental conditions.
Layer #3: Face Stock
The next layer is face stock — the visible top sheet material that consumers can see, feel, and interact with when they pick up a product with a label. Face stock refers to the layer that is decorated with brand elements, product information, and messaging. There is a wide range of face stock options available depending on the desired look that a brand is aiming to achieve, including:
Paper: Paper is the most widely used face stock, as it is the most economical and easily adaptable to various label printing methods. However, keep in mind that paper material isn’t moisture resistant or tear-proof.
Film: When durability is a concern, film is often the preferred face stock. Since film is made up of a synthetic or a plastic-type of material, it is resistant to moisture, heat, UV exposure, and other environmental conditions. Due to its flexibility, film face stock can conform to unique shapes and squeeze bottle applications.
Foil: Foil face stock consists of a thin layer of aluminum or alloy to produce a shiny, metallic appearance on the label.
Specialty Materials: To stand out on retail shelves, brands have the opportunity to explore specialty face stock materials. Examples include fluorescent papers, holographic films, and even real wood veneer.
Before selecting a face stock, it’s essential for brands first to evaluate their label needs. What type of product will the label be applied to? Will it be applied by hand or by a machine? Does the printing on the label need to withstand any harsh environmental conditions? These are all important questions to work through with an experienced Packaging Advisor.
Layer #4: Topcoat
The final layer is the topcoat — a vital step to protect the label from scuffing and damage. The topcoat adds an extra level of protection while enhancing the visual appeal with a finish. Brands primarily choose between two topcoat options: varnish and laminate.
Varnishes are thin coatings of silicon sealed over the top of the printed label, providing minimal protection against scuffing and smudging. Varnishes are typically available in gloss, matte, and satin finishes. Compared to laminates, varnishes are a more economical option. There are three main types of varnish techniques:
Flood: The varnish covers the entire printed image.
Spot: The varnish only covers a specific part of the image, maximizing contrast between matte and gloss surfaces.
Dimensional: The varnish is applied in varying layers to give the label a dimensional quality.
For a more durable topcoat option, laminates can be used to withstand smudges, scuffs, moisture, oil, and UV exposure. With the laminate process, a thin layer of film is applied to the surface of a label, providing a plastic barrier of protection. Laminates come in both gloss and matte finishes, as well as Thermal Transfer for secondary printing. Compared to varnishes, laminates offer a pronounced sheen and texture to the label.
Label Materials Play a Critical Role
In conclusion, the journey of creating a custom label is an intricate process that blends functionality with branding. Each layer—from the liner and adhesive to the face stock and topcoat—plays a critical role in ensuring your label not only captures attention but also withstands the rigors of its intended environment. Your product deserves a label that represents your brand's quality and resilience, no matter where it goes.
At The BoxMaker, we understand the importance of details in label design and are committed to helping you make the best choices for your products. If you'd like to see some of our work and get a feel for the variety of custom product labels that we can create for your business, request a free custom printed label sample kit and take the first step in elevating your product's packaging to the next level.
Subscribe
Share this post
Similar Articles
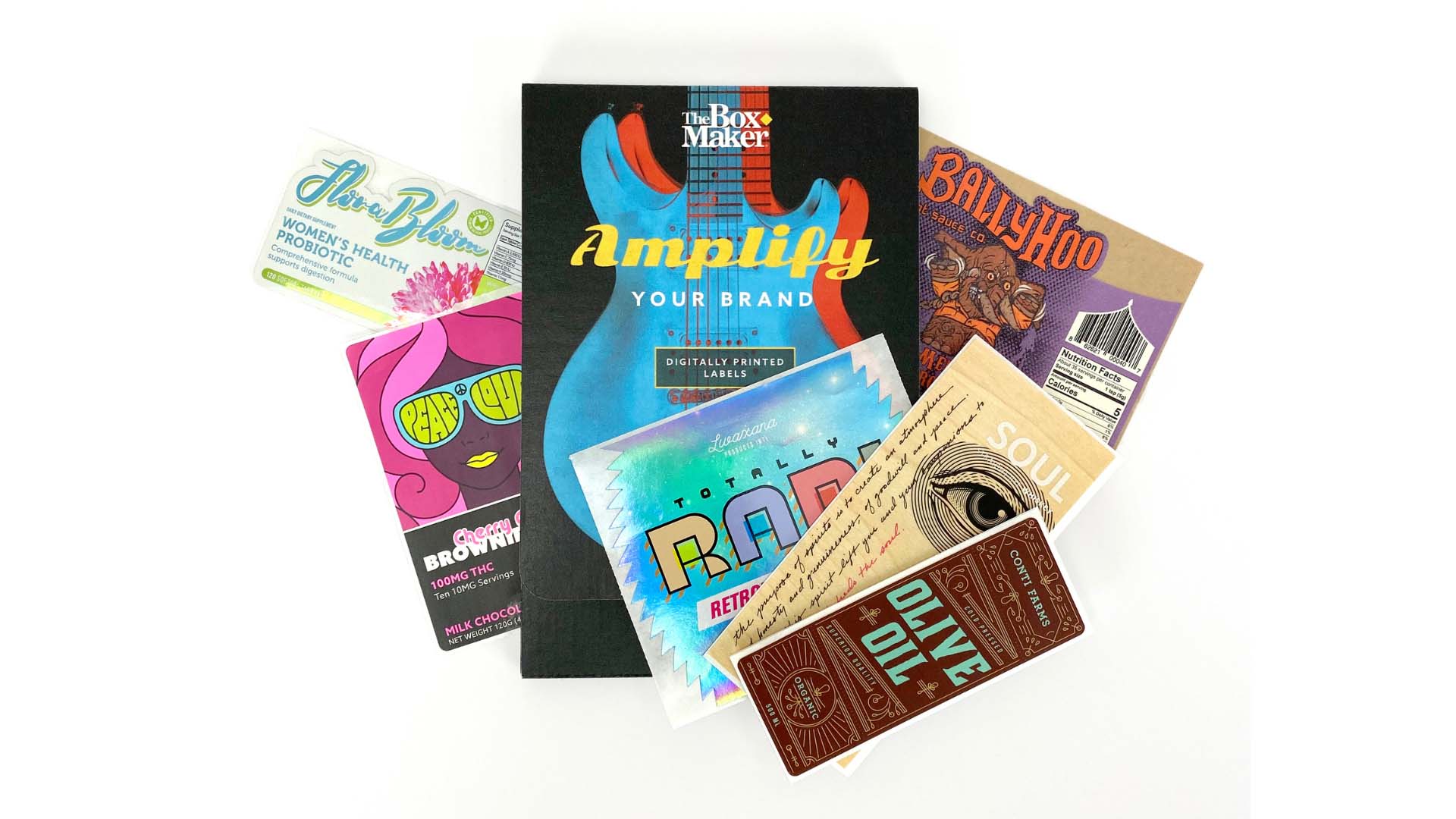
How to Design a Custom Product Label for Digital Print
Master the art of digitally printed custom labels with our guide. Explore essential steps and benefi …
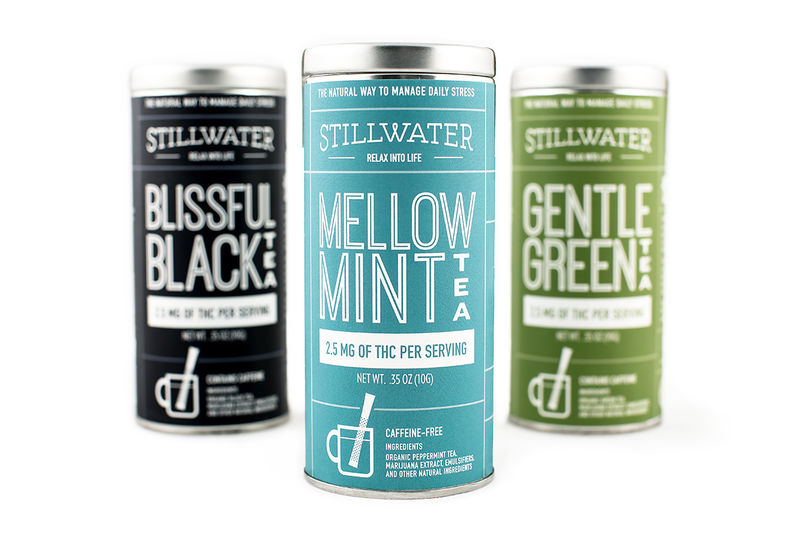
Laminate vs. Varnish Topcoat for Labels
Understand the differences between a laminate and varnish top coat for pressure-sensitive product la …
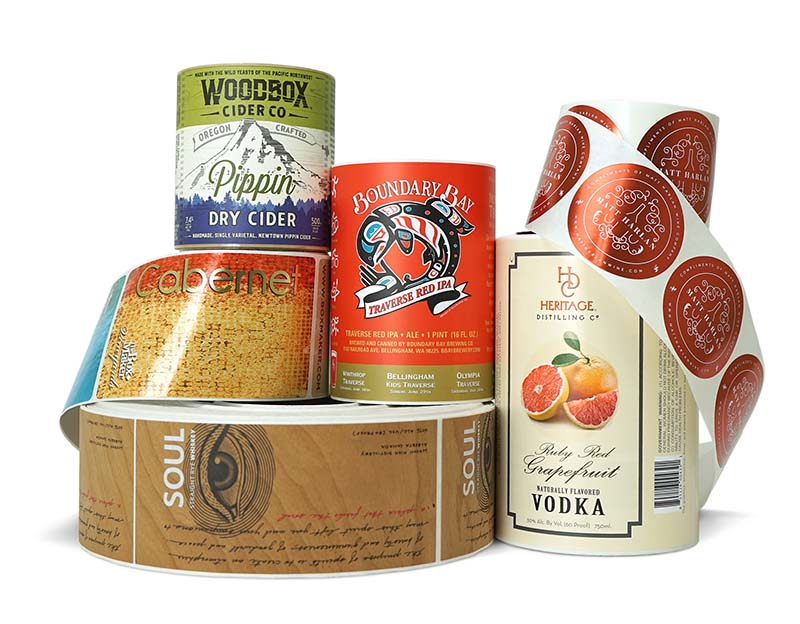
Flexo vs. Digital Print for Labels: Which Should You Choose?
Discover the advantages and drawbacks of flexo and digital printing for product labels.